Film casting
Procesos > ► Extrusión
Fundición de película
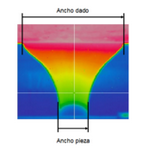
El proceso de extrusión de película fundida está ganando popularidad y goza de un crecimiento sostenido en todo el mundo. Se están instalando nuevas líneas en un número significativo y los segmentos de mercado penetrados por esta tecnología están en aumento.
Aplicaciones de extrusión de fundición
Las películas moldeadas se utilizan para el envasado de alimentos y textiles, envoltura de flores, como protectores de páginas de álbumes de fotos, como sustratos de recubrimiento en procesos de recubrimiento por extrusión o laminados a otros materiales en la formación de películas más complejas, entre otros. Típicamente, el proceso de película moldeada implica el uso de coextrusión, que es una extrusión simultánea de dos o más materiales de un solo dado para formar una película multicapa. Esto se debe a que, en muchos casos, la aplicación final de la película de plástico exige un rendimiento que no se puede lograr si la película está compuesta de un solo material. Por ejemplo, en muchos casos, las aplicaciones de envasado de alimentos requieren el uso de películas con capacidades de barrera de oxígeno. Para cumplir con el requisito, un material de alta barrera al oxígeno como EVOH se combina con materiales de poliolefina en una estructura de varias capas. Las películas coextruidas contienen típicamente hasta siete capas; sin embargo, el uso de más capas se está volviendo más común. El número de capas, su posición en el coextruido y su grosor individual son variables que cambian según la aplicación particular de la película.
Beneficios / Limitaciones de la extrusión de fundición
A diferencia del proceso de película soplada, el enfriamiento de la película con extrusión de fundición es altamente eficiente. Esto permite velocidades de línea de producción más altas que resultan en tasas de producción más altas con propiedades ópticas superiores del producto. El grado de dibujo y orientación es significativamente menor en el proceso de película fundida que en el proceso de película soplada. Esta es la razón por la distribución de espesores en la máquina, la dirección transversal es más uniforme con los procesos de fundición (con variaciones que podrían ser tan bajas como ± 1.5%). Sin embargo, las propiedades mecánicas de la película en la dirección transversal de la máquina son menores en comparación con las obtenidas con el proceso de película soplada debido al mayor nivel de orientación que experimenta la película en el proceso de soplado. En la extrusión fundida, los bordes de la película se recortan debido a irregularidades dimensionales y / o mala distribución de la capa. Como resultado, el proceso puede verse afectado negativamente si el material recortado no puede reciclarse. La tecnología reciente del sistema de matriz plana ha minimizado este problema al reducir significativamente la cantidad de material desperdiciado en los procesos de coextrusión. Este tema será cubierto hasta cierto punto en una sección posterior.
Conceptos básicos de extrusión de fundición
En el proceso de extrusión de película fundida, el polímero fundido viaja a través de un sistema de matriz plana para adoptar su forma final de película plana. El sistema de troquel está formado por el troquel y el bloque de alimentación (si el proceso requiere coextrusión) o simplemente el troquel, si el proceso es el de extrusión monocapa. El proceso comienza con la alimentación de resinas plásticas por medio de un sistema de alimentación gravimétrica a una o más extrusoras. Los materiales son luego fundidos y mezclados por los extrusores, filtrados y alimentados al sistema de troquel. Inmediatamente después de salir del troquel, la cortina fundida ingresa a la unidad de enfriamiento donde se baja su temperatura con un rodillo de enfriamiento enfriado por agua para "congelar" la película. Luego, la película se pasa corriente abajo donde se recortan los bordes, se aplica un tratamiento corona (si se requiere un proceso de fabricación como impresión o recubrimiento) y la película se enrolla en rollos.
Cast termoestables
La fundición es la técnica de procesamiento más simple: el molde se llena con un líquido que, a temperatura ambiente, tiene una viscosidad tan baja que puede llenar el molde por su propio peso. Después del llenado, debe tener lugar una reacción química para formar el material. Con los termoestables, esta es una reacción entre los componentes que, antes del llenado, se han mezclado y reaccionan en una red tridimensional. Algunas veces se agrega un catalizador para iniciar o acelerar esta reacción. Dependiendo de la combinación elegida, el curado tiene lugar a temperatura ambiente o a una temperatura elevada. Durante el curado, siempre se desarrolla calor, que no puede escapar fácilmente debido a la baja conductividad térmica de los polímeros. En el centro del cuerpo, la temperatura puede, por lo tanto, elevarse inaceptablemente alta y causar degradación térmica. Con las resinas de fundición, por lo tanto, se deben evitar las partes gruesas. Mediante una elección adecuada de desarrollo se puede controlar. Los ejemplos utilizados en la práctica son las resinas de fundición de poliéster y epoxi, ambas como sistemas de dos componentes. Los epóxicos son más caros que las resinas de poliéster, pero muestran menos contracción; La contracción, expresada como la diferencia de volumen antes y después del curado, es del 1 al 6% para los epóxicos y del 5 al 10% para los poliésteres. Las resinas de fundición epoxi se aplican con frecuencia para la encapsulación de piezas electrotécnicas como bobinas y transformadores. Las propiedades eléctricas de los epóxicos son, en general, mejores que las de los poliésteres. Las resinas de fundición pueden complementarse con cargas, principalmente con materiales inorgánicos como el polvo de cuarzo. Algunas veces esto se hace para reducir el precio de costo, pero también, para algunas aplicaciones, para mejorar las propiedades; la contracción, por ejemplo, se reduce y aumenta la dureza.
Cast de Termoplastico
Algunos termoplásticos también se pueden usar en procesos de fundición; en estos casos, la polimerización tiene lugar en el molde que se llena con el monómero. Los ejemplos son poliestireno, polimerizado a partir de estireno y polimetilmetacrilato a partir de su monómero. Estas reacciones pueden tener lugar con bastante facilidad en presencia de catalizadores adecuados. De esta manera se pueden producir láminas gruesas, pero también artículos grandes como hélices de barcos PA6 o ruedas dentadas, como productos de polimerización de caprolactama.
Geles
Los geles pueden ser un problema constante para la producción de películas de poliolefinas. En el peor de los casos, los geles pueden causar roturas de película para procesos de película fundida o pueden hacer que la burbuja se rompa para un proceso de película soplada. Este tipo de eventos aumentan el costo de producción y, a menudo, crean altos niveles de material de desecho que debe ser depositado en vertederos o reciclado. En el otro extremo del espectro, los geles pueden reducir el valor del producto o evitar que el convertidor venda películas en un mercado con mayor margen de beneficio. En la mayoría de los casos, los geles pueden mitigarse a niveles muy bajos mediante la optimización del proceso de extrusión de un solo tornillo. Tipos de gel El término gel se usa comúnmente para referirse a cualquier pequeño defecto que distorsione un producto de película. Hay muchos tipos diferentes de geles, incluidos geles reticulados térmicamente, geles altamente oxidados, geles sin mezclar y contaminación. Para los geles que se originan a partir de la contaminación, el convertidor debe poder identificar el contaminante y luego localizar la fuente. La mayoría de los fabricantes de resinas tienen la capacidad de identificar el contaminante. Sin embargo, los geles que se originan por contaminación no son el tema central de este artículo. Los geles reticulados térmicamente y los geles altamente oxidados se generan típicamente en regiones estancadas de un proceso. Aquí la resina está caliente y tiene un tiempo de residencia extremadamente largo en el proceso, y a menudo está expuesta al oxígeno. Los geles reticulados térmicamente se producen en ausencia de oxígeno, mientras que los geles oxidados se producen en presencia de oxígeno. Sin embargo, los procesos modernos de fabricación de resinas excluyen el oxígeno del sistema y son muy simplificados, por lo que normalmente no existen áreas de proceso estancadas con tiempos de residencia prolongados. Como tal, es probable que el fabricante no genere geles oxidantes y reticulados. Los geles reticulados térmicamente y los geles altamente oxidados se generan típicamente en las regiones estancadas de los tornillos de la extrusora y las líneas de transferencia. Las regiones más comunes de degradación se encuentran en los radios de vuelo en la sección de medición y en las ranuras profundas de los mezcladores. Sin embargo, muchas otras ubicaciones y fallas de diseño pueden crear ubicaciones donde la resina se puede degradar. Los mezcladores Maddock mal diseñados y los radios de vuelo pequeños son fallas de diseño muy comunes que ocurren en una gran cantidad de tornillos que se fabrican actualmente. Los tornillos sin este tipo de defectos se pueden diseñar fácilmente con poco o ningún costo adicional si el diseñador conoce las regiones de estancamiento. Dado que la resina tiene un tiempo de residencia extremadamente largo, los químicos antioxidantes no son efectivos para mitigar estos geles.